
What does "I do Lean and Kata" means?
Let's start with what it does not mean. We do not come into your organization and give you a recipe you can implement. We do not follow a mechanistic approach where we replace your processes by Lean or Kata tools hoping they perform better just because they do elsewhere. If you want someone that has all the answers and will tell you exactly what to do and how to do it, that's not us.
​
Instead, we will help develop your people by solving problems to improve your processes as we strive towards goals that will move your organization in the direction you want to take it. Lean and Kata are about developing a learning organization that can ensure its long-term survival by constantly improving and adapting to new challenges. That's what we will strive for from day one.
Besides, you're different. Every organization is, and that requires that we customize Lean and Kata ideas to your needs, bringing them in only when needed as we strive to solve the specific problems you're facing.
​
We don't bring solutions. We only bring experiments that we can run together to learn what works for your organization and what does not. By keeping what works and refining it, we will evolve a Lean system customized to your needs.
But what is it all really about?
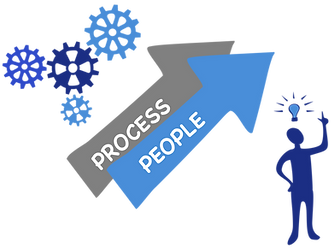
DEVELOP PEOPLE AND PROCESSES IN PARALLEL
We will develop your people by coaching them to solve the problems they encounter as they strive to improve their processes in pursuit of challenging goals. We want stable processes that can satisfy current needs and we want people that can continue to improve them to help the organization succeed in the changing conditions that the future will bring.

STRIVE FOR FLOW
At the most general level, we want to create a steady flow of value to the customer. Striving to improve flow helps build the scaffolding for processes and mental models that will enable the evolution of a true Lean system. It also can help us see opportunities for improvement we can use to drive the Lean evolution.

UNDERSTAND THE DESTINATION
Where do you want to go? What do you want or need to achieve?
Starting with a clear idea of the end in mind ensures we focus and prioritize our efforts on the issues that matter the most.

UNDERSTAND WHERE YOU ARE
What's the current condition with respect to where you want to be?
There's no need to understand everything about the organization, but we do need to understand deeply the current situation of the processes affecting the goals we want to reach.
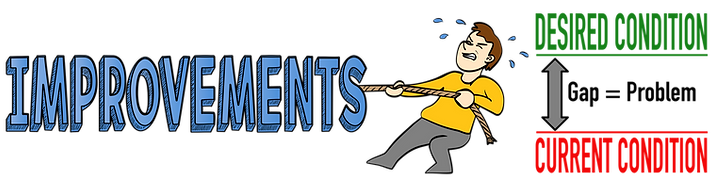
PULL IMPROVEMENTS
The gap between the current and desired conditions defines the problem we need to solve. We use it to pull only the improvements needed, when and where they are needed. It's not about applying Lean tools across the board. It's about overcoming the specific obstacles preventing us from achieving our goals. A Lean system, customized to the needs of the organization, will evolve as processes improve and people grow.
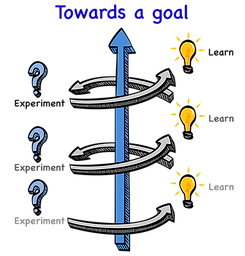
EXPERIMENT AND LEARN
We will solve problems by engaging your team and coaching them to think scientifically. Every organization is different and faces different challenges. We can learn from what others have done, but that will take us only so far. To develop sustainable solutions we have to find our own way through experimentation and learning. We keep what works and continue to refine it.

CAPTURE LEARNINGS
Long-term sustainable success requires the organization to evolve, so we need to capture individual learning into organizational learning by changing the physical process, including it in SOPs, and/or sharing it widely with other people.

CONTINUOUS IMPROVEMENT & PEOPLE DEVELOPMENT
And then we do it all over again. Every day, every week, every month, every year... involving everyone in the organization. Continuous improvement never ends. It builds on itself, developing people and processes and taking the organization to ever higher levels of performance.